Author |
Message |
   
Bill Vatter
Frequent User Username: bill_vatter
Post Number: 30 Registered: 9-2004
| Posted on Tuesday, 03 October, 2006 - 20:05: |    |
I have a rear spring from my Mk VI Bentley on the bench for cleaning and polishing the spring leaves. (I also need to return a cobbled-up bijur line to original configuration and rebuild leaking rear shock dampers.) What about spring lubrication? Two very experienced individuals (mostly prewar experience) who have cared for many cars for many years have opposed opinions. One says use synthetic grease between the spring leaves, but the other says use only oil, no grease. The first says the Bijur oil isn't going to get into the springs to any significant degree, and the second says must not use grease because it will impeed the distribution of oil inside the spring. Really it does not appear that much oil is going to go into the spring from the Bijur. It looks like the excess oil just drips out at the ends of the shackle pins. Maybe not much oil is needed. It is really not possible to tell what has been in there before. It is rather like grease now, but that is a grease made by mixing oil and dirt. No one recommends that. Other opinions with reasons and logic are solicited. |
   
Bill Coburn
Moderator Username: bill_coburn
Post Number: 738 Registered: 4-2003
| Posted on Tuesday, 03 October, 2006 - 21:59: |    |
Bill as far as I am aware the springs on a Mark VI are not that much different in design to those of a Cloud or Phantom. The latter two models I recently de-gaitered and both lots of leaves are dry. Of course there is no oil dribbler to have them otherwise. In my day (leans back and takes a long draft of the Meersham) greased springs gave a great ride even if a bit bouncy but were also a recipe for broken leaves since the shocks of yesteryear were not particularly controlling. The argument of grease vs oil brings out the cynic in me as I remember the awesome pronouncements as various bits of the early Clouds were finally greased and the oil dispensed elsewhere. Yet the parts lubricated did not change??? Mark VI owners can be reduced to apoplexy if you suggest throw out the Bijur system and insert grease nipples. Personally when I had my Dawn I used the one shot oiling and blanked off that idiotic supply to the clutch throwout bearing. But at the same time I almost got through more oil in the one shot than petrol in the tank (I exagerate slightly). But oil the various bits I certainly did. When you look back on it - how ridiculous to expect an owner to religously keep that pedal pressed in a car that cost 4 times that of a contemporary Buick!!! The feed of oil to the springs on a Mk VI as I remember was via a small tube that connected the interstice between the shackel pin and its bush so that excess oil flowed down in delicate cascades from leaf to leaf. What an absolute wank. The tube blocked up about the time the guarantee expired and due to the design of the springs and suspension worn shackels which invariably occurred were not apparent until they were at the dangerous stage. If I had a Mk VI now I would rig up my engine oil tester to the tee piece under the Bijur pump fill it with oil and throw about 50 psi of compressed air into it and see where the oil came out. The reason I should have mentioned that I would keep the system is that that was how the car was bloody well made! So if I had your springs out I would cram them with a high melting point very sticky grease as advised by your local purveyor of lubricants and if the oil manages to find its way down that little hole all power to it! I hope that the reasoning is clear - I cannot vouch for the logic. |
   
Stephe Boddice
Experienced User Username: stephe_boddice
Post Number: 44 Registered: 2-2005
| Posted on Wednesday, 04 October, 2006 - 09:58: |    |
Oh dear! Two Bills for a Rolls-Royce can prove to be very expensive. Bill C's posting for the Mk VI manual do not appear to contain a chassis diagram for the One-shot system. Being a pre-war Luddite I offer myself for verbal execution for the following observations. On the pre-war chassis the Bijur system had two supplies at the shackle pins: one fed the pin and the second pipe was run along the top of the upper leaf. Each leaf has a fine groove and through-drilling to allow oil to work down through the leaves. The assumption was that the gaiters keep out all of the dirt so there is never any contamination. As the pre-war chassis that had this system are now at least 60 years old - and still working - it would seem that the thinking was pretty sound. Most other manufacturers use exposed leaf springs with no lubrication or protection whatsoever and their cars still work fairly well. You pays your money and... SB www.boddice.co.uk |
   
Richard Treacy
Grand Master Username: richard_treacy
Post Number: 1091 Registered: 4-2003
| Posted on Wednesday, 04 October, 2006 - 20:42: |    |
Stephe, The early postwar cars are little different. The spring lubrication is via the shackles, and as you note the oil is supposed to dribble down the grooves in the leaves if you are lucky. Having said that, I have broken a dozen leaves on my R-Type. A very nice Aboriginal guy called Jonnie at Jones Springs in Newtown, Sydney, used to make all the (numerous) replacements for York Motors before Jones retired and Jonnie moved to Lovells Springs not far away in Parramatta Road. They copied the originals, tapers grooves and all. The Lovells factory has since moved to Minto I understand. Jonnie was always very understanding of me surprise surprise. The leaves always broke at the clamp rivets, so we eventually did two things to find a proper solution. First, instead of riveting the clamps I had new ones made and used Loctite to secure them and to eliminate the stress regions. Secondly, I packed the leaves with the silicone grease recommended by Lovells and triple shrink-wrapped them with industrial-grade stuff. The shrink wrap stops the grease from escaping and stops the gaitors from rotting in the bargain. Lovells preferred to use plain spring leaves with nylon interleaves and run them dry as on most other vehicles, but agreed that the sealed solution with tapers and grooves with lubrication is a viable option. This all seems to have done the job as no leaves have broken in the 20 years since. It may not be to everyones’ liking, but it works for me. The attached scan is part of a package of late MkVI and R-Type manuals due in our library once the scanner stops smoking.
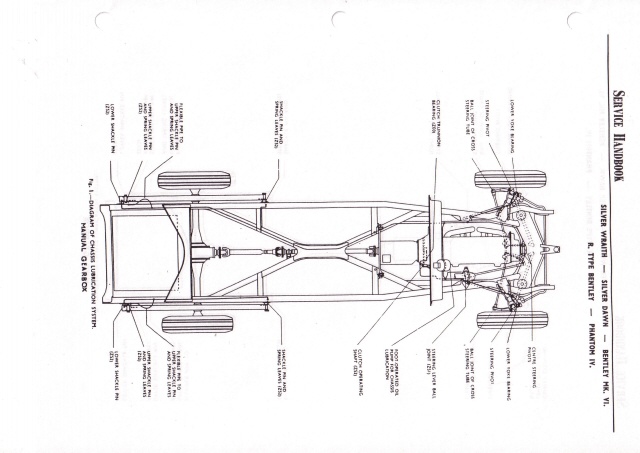 |
   
Richard Treacy
Grand Master Username: richard_treacy
Post Number: 1093 Registered: 4-2003
| Posted on Thursday, 05 October, 2006 - 06:38: |    |
In downloadable PDF form:
|
   
Laurie Fox
Experienced User Username: laurie_fox
Post Number: 21 Registered: 6-2004
| Posted on Friday, 06 October, 2006 - 10:09: |    |
I don't suppose that this post will throw much light on the spring lubrication question but I have been prompted to look at and photograph a broken top leaf from my MK VI (rear offside). It was replaced some years ago and I have kept it, without cleaning it up, because I thought it could possibly provide useful information later on. It had done 397451 miles. The bit that I was able to keep is the bit which was attached to the front shackle - I just watched as the job was done professionally. The front shackle pin was still quite serviceable and was not replaced. There was oil in the bush (not very clean, admittedly) which had lubricated the bush and pin very well but the feed to the spring leaves was bunged up. The next picture shows that the bush was not dry
The next picture shows that the break was at a point between the first and second clip.
The next picture shows the underside of the front eye
The next picture shows the topside of the front eye
The next picture shows the wear under the front eye caused by the second leaf
The break has rusted quite a bit now but at the time it was a clean break without any sign of progressive opening up over a period. So what are the loads on the spring leaves under various conditions? Before the spring was rebuilt the leaves were wirebrushed and laid out on the floor. All seemed to be OK with more curve in each lower leaf than in the one above as I think it should be. So when the spring had been assembled each leaf would be pressing, mainly at it's tip, on the one higher up - just like it was originally. The marks of the underside of the top leaf seem to suggest that it is only the tip of the lower leaves which press on the upper leaves to any significant extent when the spring is on the car. But as the car rides over bumps the ends of the lower leaves will move forward and back relative to the next higher leaf with more movement from the larger bumps. This movement is a rubbing action which, dependent upon the lubrication at those points, will eventually wear both the higher and the lower leaf. Look at the last picture again. The lower leaf has worn the upper leaf where it has been in contact, has removed a significant amount of metal from the top leaf and left a pronounced ridge at the end of its normal travel. Do not confuse this ridge with the brighter marks neared the top of the picture which are the marks made by the second leaf after the top leaf had broken. When the top leaf broke it was held by the spring clip and more or less stayed in place although the second leaf was than touching it nearer to the eye, causing the bright patch in the picture and pushing up the oily dirt nearer to the spring eye. Now the shape of the oily dirt ridge suggests that the second leaf had a fairly sharp edge. This sharp edge would have been moving to and fro in normal running and gouging out metal from the top leaf. But normal running over ordinary roads with minor bumps and undulations would not have cause the second leaf to move very far so the ridge which it formed would be only part way to the point of full deflection. When a big bump comes along the end of the second leaf will have to climb over the ridge. In doing this it will try to push the top leaf forwards and thus push itself backwards which will cause tension in the top leaf in addition to the other loads on the top leaf at the time. Whether this additional tension had any real bearing on the failure we don't know. But it does bring out a possible point of weakness in spring leaves which have this kind of wear. I think that, had I known this at the time the spring was rebuilt, I would have chamfered the front edge of the second leaf (and possibly the others too) so that it would ride up over the ridge more easily. I don't think that I would have been tempted to grind the ridge out of the top leaf. Clearly, some form of lubrication of the leaf ends is desirable and some form of wrapping and/or gaiters may well be the answer. I have had two sets of gaiters on B420EY but eventually they disintegrated and towards the end of their life they merely became dangling mud traps which prevented me checking the spring leaves so I now run without them. (Message edited by laurie fox on October 06, 2006) |
   
Bill Vatter
Frequent User Username: bill_vatter
Post Number: 31 Registered: 9-2004
| Posted on Friday, 06 October, 2006 - 13:11: |    |
I have my spring disassembled and I see now thereare oil holes and distribution grooves to lubricate the top 5 leaves (9 total). Clearly some kind of grease should be applied to the lower leaves that do not get Bijur oil. Possibly a think coat of grease on the wearing surfaces might also be in order for the other leaves, taking care that the grease does not plug the oil distribution holes and grooves. Like the others, my oil holes were filled with crud, blocking their effectiveness. It seems like oil distribution should work, as long as the distribution path does not get plugged up. Not using the Bijur regularly might do that, as might also standing unused for a long period. Routine use on wet roads could promote corrosion. I wonder how many years/miles of careful use will it take before the oil holes again become plugged and the spring performance again deterioriates. This is a miserable dirty job, and not one I would want to do frequently for the enjouyment of the work. |
   
David Gore
Moderator Username: david_gore
Post Number: 652 Registered: 4-2003
| Posted on Friday, 06 October, 2006 - 13:23: |    |
Hi Laurie, This has aroused my curiosity given Stephe Boddice's observations and the fact that leaf spring technology was relatively mature by the 1950's. If possible could you please photograph the actual fracture face on the spring leaf from the closest distance you get keep it in focus and post it on the forum - I will mark up areas of interest for more detailed photos and email back to you. Please do not try and clean-up the fracture for appearance purposes. Can you remember at what time of the year did the spring fracture? |
   
Bill Vatter
Frequent User Username: bill_vatter
Post Number: 32 Registered: 9-2004
| Posted on Friday, 06 October, 2006 - 13:24: |    |
Also thanks to Laurie who verified the top most leaf is much straighter than the others. You need to have large C clamps on the spring stack when you remove the spring clamps. It appears thet the residual force from the top leaf, which is much sturdier (thicker)than the others is under diferent preload than the others when the spring is in its unloaded state. When a bump hits, the top leaf unloads and then loads up in the other direction while the other leaves simply increase load in the same direction they are preloaded. That would create a variable rate in the spring, soft, but becomming stiffer as the spring deforms. Ingenious, but possibly just the way it has always been done with RR being not the first to use such a variable rate spring. Is this the secret of the excellent ride provided by RR cars that are in very good condition? The top leaf also natrally deforms less than the others, possibly with the purpose of avoiding excessive stress in the leaf that carries all of the weight on it's ends. |
   
Laurie Fox
Experienced User Username: laurie_fox
Post Number: 22 Registered: 6-2004
| Posted on Saturday, 07 October, 2006 - 03:11: |    |
Bill Here are some further thoughts. I agree that when the spring is assembled, and bolted up before it is fitted to the car the top leaf and possibly one or two of the ones immediately below will be pushed upwards, tending to make them more curved. But when the spring is in the car and taking the standing load from the wheel the top leaf is virtually level. The initial unloaded curvature of the top leaf and any extra curvature from the lower leaves has been removed and the bending moment in the top leaf will be trying to raise the spring ends relative to the rear axle. This will continue to apply on a bump which raises the axle from it's normal position. If the car then rises and the rear axle drops relative to the car it may go down as far as the lower bump stop. Let us assume that it does. The spring will then be in the most unloaded position available to it and the top leaf may or may not have reached the point where the bending moment is in the reverse direction. This will depend on how much movement is possible before hitting the bump stop. The end of the top leaf is taking part of the weight of the car, say 450 lb for the sake of this discussion. Let us assume that the eye is 27" from where the spring assembly is clamped to the axle and that each of the eight lower leaves touches the one higher up 3" behind the tip of the higher one. If the second leaf is pressing upwards with 400 lb the top leaf is getting support which will reduce the bending load (bending moment in mathematical terms) on the top leaf between that point of contact and the axle. Likewise the third leaf may be pressing 350 lb on the second lead and so on. In this way the 450 lb load would be shared between all the leaves equally and the total bending load (450 lb multiplied by 27 inches) would be shared in a similar way. The spring designer may well adjust the leaf thickness, leaf length, unloaded curvature etc. to keep everything working within the elastic limits of the material but the principle remains the same. Then, in addition, the spring designer has to take into account the fact that the top leaf is the one which holds the axle to the car. On the MK VI, driving and braking forces go through the front of each top leaf to the front shackle and these are not just horizontal loads. Heavy braking probably gives the worst conditions where the rear axle will want to rotate by dipping the prop shaft and will be held by the front of the rear springs bending more and the rear of the rear springs bending less. Provided the lower leaves remain in contact with the higher ones over the whole deflection range then the whole assembly should behave as the equivalent of a single spring with no variable rate. Some truck springs provide a variable rate by having substantial lower leaves which the upper leaves only contact after some initial deflection. Regards Laurie
|
   
Laurie Fox
Experienced User Username: laurie_fox
Post Number: 23 Registered: 6-2004
| Posted on Saturday, 07 October, 2006 - 08:00: |    |
David Some details about the fracture and the pictures herewith. When did it happen? January 2000, winter of course in UK. I don't remember any particular bump or pothole which may have caused the break but I did become aware of unusual steering which I investigated quickly and discovered the break which must have happened shortly before. The broken top leaf did not come completely adrift but the location of the rear axle had been impaired and there was some rear wheel steering going on as the axle on the right hand side moved an inch or so forward and back under driving and braking loads. The broken end of the top leaf (the one in the pictures) did not touch anything on the car. But there is a small mark (flat, looks as if it had been hit with a hammer) on one end which may have been made when getting the broken leaf out. The fracture initially had no rust at all anywhere but has accumulated a bit of rust from the rag in which it was wrapped and then left untouched. The photos were taken with tungsten lighting from a reading lamp so that I could direct the lighting and have been roughly corrected for colour balance. The originals were cropped to about 1300 pixels wide to about 950 pixels wide before being reduced to 500 pixels wide for this post. There seems to have been very little loss of detail but the originals (as cropped) are available and I can send you the files if you would care to see them. Most of the pictures show the underside of the leaf uppermost in each photo. Where the top side is uppermost in the photo I stuck a little "top side" label on. Over to you. Regards Laurie
Picture 1, above
Picture 2, above
Picture 3, above
Picture 4, above
Picture 5, above
Picture 6, above
Picture 7, above
Picture 8, above
Picture 9, above
Picture 10, above
Picture 11, above
Picture 12, above
Picture 13, above
Picture 14, above |
   
David Gore
Moderator Username: david_gore
Post Number: 655 Registered: 4-2003
| Posted on Sunday, 08 October, 2006 - 11:55: |    |
Hi Laurie, Thank you for a very professional and informative set of photographs. My initial observations are as below: 1. Refer picture 10. The smooth region on the top LH corner is a classic fatigue crack originating from the corner. Picture 14 appears to show the characteristic striations that are usually present in cracks of this type and I would like to see an enlarged view taken from the same positions as pictures 10, 11 and 14 to confirm this. 2. The final catastrophic failure has occured instantaneously and is most likely brittle fracture associated with the steel composition/heat treatment - the ambient temperature at the time has been below the ductile/brittle transition temperature for the spring material. It is also possible internal defects in the metal have contributed to the problem however this can only be confirmed by microscopic examination. 3. The failure has occured when the spring leaf was being pushed upward by suspension loading, the final fracture originated under tension at the base of the existing fatigue crack and propogated initially across the full face of the spring cross-section. This weakened the spring such that the bending was then localised to the plane of the crack instead of being uniformly distributed along the length of the spring. This is why the bottom edge of the failure shown in pictures 10 to 14 has gone under the top fracture edge. Note to Richard Treacy, did your R type spring problems usually occur when it was cool or did they also occur in summer? Based on your comments about the influence of the clamp rivets on the cracking, these would certainly have acted as stress concentrators and if the spring material/heat treatment was not appropriate, brakage was highly probable. |
   
Richard Treacy
Grand Master Username: richard_treacy
Post Number: 1094 Registered: 4-2003
| Posted on Sunday, 08 October, 2006 - 21:33: |    |
David, I can't comment on cold vs hot weather as broken leaves with the stiff Australian-spec springs do not show any signs for months, the leaves being covered by the gaitors. I remember always changing them in Summer time, but that means nothing. The two large rivets (3/8"?) in each clamp simply reduce the strength at those points enormously. None of the breakages was ever like Lauries. They always appeared to have started with a clean break through the rivet hole centres for the front clamp, causing a chain reaction through the other leaves directly above over time. As only the leaves' ends broke off, the standing height loss was only detectable once the concentrated load at a single point on the main leaf caused plastic bending once all the leaves below had broken. I would not put this down to fatigue. Compare it to a wooden ruler. No fatigue there. Bend it as much as you dare without breaking it. Drill a pair of holes in it and bend again to the same extent. Snap ! York Motors were always very busy changing pre-Silver Shadow leaf springs on cars used primarily out of the city. By contrast, I have only ever had one broken front coil spring on the R-Type (1971 and about 250,000 miles): it was the front left of course, presumably due to the rough shoulders on the Hume Highway at the time. That was no doubt a fatigue issue. See those silly clamps below, riveted to the lower leaves. The one at the left was always the culprit, hence the Loctite solution. In a case of marginal design failure like this, I don't believe in playing at the margin with lubrication grades or worrying about a few tens of degrees in temperature range. Only a solution with a decent safety margin will do.
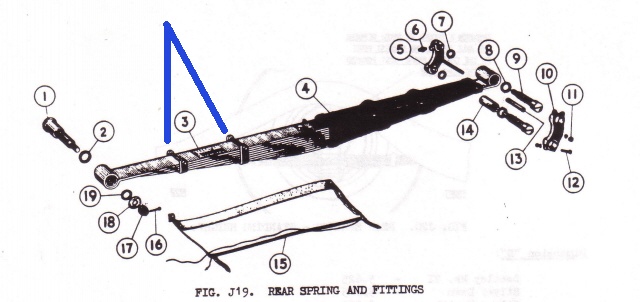 |
   
Laurie Fox
Experienced User Username: laurie_fox
Post Number: 24 Registered: 6-2004
| Posted on Monday, 09 October, 2006 - 08:41: |    |
David Your initial observations are most interesting. I have done some more photos, using a jewellers loupe as a close up lens on the camera which seems to have worked quite well. There are four sets, each comprising three pictures, with slightly different lighting for each set. All are of the top edge with the top of the leaf uppermost in each picture. As taken, each frame is 2048 by 1536 pixels and has been roughly colour corrected. These have been reduced to 500 pixels wide for the bulletin board. I have added a further picture at the end showing the kind of detail available before size reduction. Would you like me to send you any (or all) of the 2048 by 1536 frames? Each frame is only about 300,000 bytes as a .jpg file. I am intrigued by the effect of ambient temperature on steel. I know that some of the cranes unloading ships in Helsinki are only rated for about 2 tons although they look very substantial indeed and that Valmet, also in Finland. were very concerned about the steel which they used for tractor gearbox gears in order to keep tooth breakage down. Because of this temperature effect I cannot help thinking(with my joke hat on) that this has a slight connection with the gaiters or no gaiters question. Gaiters on retains the small amount of warmth generated by friction between the spring leaves whereas gaiters off permits warmth from heat radiated from the exhaust pipes (one side only, of course, on 4 1/4 MK VI's!). I suspect that there may well have been an inclusion or something in the top leaf material at the point where it actually broke since the bending moment at that point is not as high as it is elsewhere along the leaf. I don't think that it is of sufficient importance to justify examining further since I don't think that this is a common fault. But since small surface defects can act as stress raisers is there any advice which can be given to Bill regarding the degree of polish etc. which he could apply to his spring leaves. Does wirebrushing to remove rust leave pock marks which should be removed in some way and if so how? Regards Laurie
Set 1 left above
Set 1 centre above
Set 1 right above
Set 2 left above
Set 2 centre above
Set 2 right above
Set 3 left above
Set 3 centre above
Set 3 right above
Set 4 left above
Set 4 centre above
Set 4 right above
Set 4 left magnified above |
   
Bill Vatter
Frequent User Username: bill_vatter
Post Number: 33 Registered: 9-2004
| Posted on Tuesday, 10 October, 2006 - 05:19: |    |
Richard, You refer to "stiff Australian-spec springs." My Mk VI chassis card shows rear spring poundage "near 1075" and "off 1150." The little brass plates on the springs corresponds to this. The springs have 9 leaves. Do these sould like "colonial specification" or what would have been used on a home delivery car? My car, B340DA, was delivered new in Southern California, and lived there all its life there. That is not a rough life, and I wouldn't think they would have used colonial specs on the car. |
   
Bill Coburn
Moderator Username: bill_coburn
Post Number: 752 Registered: 4-2003
| Posted on Tuesday, 10 October, 2006 - 08:07: |    |
Well Bill like Australia, you people did start out as a 'colony'. Habit dies hard! Another little quirk we were subjected to at the time was in cricket. Players of the 'Home' team were always referred to by the English commentators as 'Mr' Brown but the Aussie team members were referred to as Smith or Jones etc. Colonial springs indeed!!! How's that for off topic! |
   
Laurie Fox
Experienced User Username: laurie_fox
Post Number: 25 Registered: 6-2004
| Posted on Tuesday, 10 October, 2006 - 08:14: |    |
Bill and Richard There seems to be something odd about the "official" instructions for matching various rear springs to individual cars. The spares schedule says that there are 7 different springs available and gives a part number for each. The poundage for these part numbers is given as 1050, 1100,1150,1200,1250,1300 and 1400. The Service Handbook gives figures for what the standing height should be, with some tolerance permitted, and says pick a spring that suits (there is no other way of altering the standing height). Maybe that is what was done when Bill's car was assembled and it so happened that a spring marked 1075 had a bit more curve in it than some of the others and happened to give the correct standing height. I can't imagine any other reason for the seemingly large difference between the two spring poundages. There is some suggestion, in the spares schedule, that some of these springs are slightly deeper in the middle, probably because they have more and/or thicker leaves - fair enough. We are led to assume, because it is not stated otherwise, that the springs with the greater poundage rating are correspondingly stiffer. So what is a "colonial spring"? Is it just one of the higher poundage springs which gives a higher standing height than normal or is it a special spring not listed in the spares schedule? Regards Laurie |
   
Richard Treacy
Grand Master Username: richard_treacy
Post Number: 1097 Registered: 4-2003
| Posted on Tuesday, 10 October, 2006 - 08:57: |    |
Sorry, Bill V, I cannot give any definitive answers until Christmas as my R-Type is far away from here, unless Bill C. sneaks around with a flashlamp and a switchblade before dawn to where the car is located not far from his own home ! However, wouldn't the 4th of July have eliminated US eligibility for anything Colonial ? More seriously, maybe Norman could clear this up. I do remember that The Colonial rear springs on B174UM have fewer leaves of a thicker grade than those delivered to the US and the UK: maybe five to seven leaves ?? Please be aware that the minimal changes I apply (slight prelube of the springs with a smear of leaf lubricant from Lovells, Loctited clamps rather than riveted clamps, and shrink wrap) are not a recommendation, but they work fine for me. My Bijur works perfectly, but it took quite some years of adjustment to get it all correct. I don't believe that many left the factory properly set up, and as a school kid I used to help my father fiddle around with a range of restrictors and various one-shot valves kindly given to us by York Motors. I still have a box full of a few dozen new and used ones in my shed back home. The trick is always to be sure that, simultaneously, the front suspension yoke lower bearings are moist (meaning that, by its design, the king pins are lubricated before the yokes are oiled), that the rear springs show some moistness at the rear axle mounts, and that there are no drops of oil on the garage floor. Those factors show the Bijur to be working well without destroying rubber components or causing the wrath of those of us who do not tolerate any oil deposits on driveways. RT. ps for Laurie: on all postwar cars up to the end of the Silver Shadow II, Colonial Springs were provided front and rear for certain markets like Australia. A MkVI with Colonial springs is quite different to drive from a Home Market vehicle. In each application, the standing height is unaffected, but the spring rate is markedly higher. This was so much so that Silver Shadow and Silver Shadow II cars with these springs had the rear antiroll bar deleted in their original build specification. The roll stiffness is increased so much that the rear antiroll bar would have caused even more skittishness than on the home market cars where it is only just acceptable. In the S-Series / Silver Cloud range, the Colonial springs changed the behaviour so much that the Z-Bars were removed from many cars with those springs in service to balance the roll stiffness front to rear. |
   
Bill Vatter
Frequent User Username: bill_vatter
Post Number: 34 Registered: 9-2004
| Posted on Tuesday, 10 October, 2006 - 11:00: |    |
Laurie, I think different spring poundage left and right is common, with the heavier one on the driver's side. 75 more pounds right rear is half the weight of a 150 lb. driver. I also think spring poundage is really two numbers. The specified poundage, and what was put on the car. The chassis notes state ACTUAL poundage (emphasis mine). I have this vision of spring makers putting springs together, testing them to determine actual poundage, engraving that on the ID plate, and sending them off to the car assembly department. The other half of this picture is the assembler selects springs from a group of many. He is looking for a 1050, doesn't find that but sees a 1075, which he puts on the car and records that. As evidence to the above, the specification card for my Silver Wraith states "LH 1200 RH 1300" for "road springs." The data sheet that I think followed the chassis as it was being assembled, records Road Springs Poundage rear: near 1239 off 1330. This is the sheet that lists the serial numbers for a multitude of components fit to the car. Not exactly rocket science there. The fitters simply put on whatever was close at hand. The reason I am into the springs is the car rode like a truck. At first I thought, Oh this is a Bentley, sporty suspension and it's supposed to be bouncier than my Silver Wraith. After being bounced and jerked for about a year, I decided no one would really want a car like this; it must have colonial springs. Finally I drove a car with overhauled springs, and that opened my eyes. Then I went asking around to find out what was wrong with my car, and several people told me, "Oh, your springs are all crudded up. Take them apart, clean out all the rust and dirt, polish up the leaves and oil them, and you'll be fine." I am just wondering what kind of ride to expect when I'm done. |
   
David Gore
Moderator Username: david_gore
Post Number: 656 Registered: 4-2003
| Posted on Tuesday, 10 October, 2006 - 13:09: |    |
Hi Laurie, My apologies for the delay in responding due to an ongoing series of demands on my time that I could not escape. Also my thanks to those who have provided additional information. It has always been my understanding that R-R Motor Cars increased the spring deflection resistance on the driver's side of the car to compensate for the weight of the driver. Would you please send me your email address using the "Contact" Utility and I will advise my email address for you to send full size versions of the following photos: Set 1 left Set 2 left Set 3 left Set 4 left Set 4 left magnified I am 99% certain the spring has failed by metal fatigue creating a notch leading to brittle fracture associated with the metal being below its ductile/brittle transition temperature. I have identified the starting point of the fatigue crack but wish to confirm this from a higher resolution image before posting this opinion. Steels can have a wide range of ductile/brittle transition temperatures determined by both their alloy composition and heat treatment. Metallurgists and engineers usually collaborate on material selection and heat treatment specification to meet the demands of the service stresses, shock loadings and anticipated service temperature range likely to be encountered by a critical component. The textbook reference to the importance of ensuring the ductile/brittle transition temperature is below the lowest ambient temperature encountered in service for critical components is the experience of the US-built "Liberty Ships" during World War 2 when the early ships began breaking in two when they encountered low temperatures during winter convoys in the North Atlantic Ocean. The problem was solved by changing the grade of steel used for the hull to one which had a lower ductile/brittle transition temperature. |
   
Laurie Fox
Experienced User Username: laurie_fox
Post Number: 26 Registered: 6-2004
| Posted on Thursday, 12 October, 2006 - 04:02: |    |
Bill When my springs were sorted out they were reassembled with some fairly ordinary grease lightly applied to the leaves. We did not clean out any of the oil holes and grooves apart from what the wirebrushing did. I did not notice any difference in the ride afterwards but I must confess that I was not really thinking about that aspect of things at the time so there may have been a difference but not large enough to draw my attention. It will be interesting to see what you find. My one shot lubrication certainly looks after the shackles very well and the small amount of excess oil tends to go down the sides of the leaves to a sufficient extent (probably) to stop water getting in from the sides. But the undersides of the leaves are exposed to the weather, since there are now no gaiters on B420EY, so the main loadbearing parts of the lower leaves are not really lubricated at all. But we must not forget the rear shock absorbers. They certainly have a lot of load to cope with judging from the fact that the rubbers in the linkage on B420EY lead quite a hard life and need changing occasionally. Also Rolls stiffened up the shock absorber fixings to the springs at the later part of the E series which means that my shock absorber linkage differs from yours. My ride control makes a significant difference to the ride, particularly at the higher speeds, and I usually run with the setting at about the middle of the range. What kind of difference to the ride do your ride control settings make? Regards Laurie |
   
David Gore
Moderator Username: david_gore
Post Number: 660 Registered: 4-2003
| Posted on Thursday, 12 October, 2006 - 17:01: |    |
Laurie kindly forwarded his images to me and the following photograph is my best opinion on where the failure was initiated:
The initial crack started most probably from a seam or non-metallic inclusion at or just below the surface. Another possibility is the presence of surface decarburisation [always a potential problem with spring steel] due to an excessively oxidising heat treatment furnace environment prior to quenching. The final determination of the cause would require cutting samples from the spring for microscopic examination. The technique of shot peening [not grit blasting]has been an effective way of reducing the incidence of fatigue crack initiation in materials subject to cyclic stresses. This involves using metal shot to peen [i.e. hit the metal surface hard enough to cause deformation] the springs after heat treatment to induce compressive stresses in the surface of the spring which will act to reduce the tensile stresses induced at the surface from bending of the spring in service. If you have access to a competent shot peening facility, I suggest it would be beneficial to have all the spring leaves individually shot peened before reassembly. However, I fear that this kind of specialist facility is no longer commercially viable and access to a large scale industrial plant will be necessary. Ooops - forgot to mention the best source of information on where to find a shot peening facility would be a manufacturer/supplier of metal abrasives [steel shot and grit]. (Message edited by david_gore on October 12, 2006) |
   
Bill Vatter
Frequent User Username: bill_vatter
Post Number: 35 Registered: 9-2004
| Posted on Friday, 13 October, 2006 - 04:20: |    |
Laurie and Richard, Richard indicated that when everything is right, you should see oil dampness at the center of the springs near where the axle bolts on and not elsewhere. You suggested possibly oil is coming out elsewhere on your car. As I further study what is happening at the shackle pins and bushings, it is now pparent that there should be no appearance of oil at the shackle pins, except possibly the lower rear pin. For the upper rear and front shackle pins, the oil enters through the inside of the pin arriving at the bushing-pin interface in the center. The threaded bushing and pin receive some oil, but the majority of the oil passes out and into the oiling system of the holes and grooves within the spring, distributing oil to the leaf-leaf interfaces from inside. Therefore if you see oil driping out of the front and rear upper shackle pins, that is good news and bad news. The good news is the bijur is delivering oil to the shackle pins and they are getting oiled. The bad news is the oil passages inside the springs are plugged up and the springs are not getting lubrication. There are rubber seals on each end of all shackle pins, which may or may not still be alive. However, if the spring oil passages are plugged up, the oil would be forced out at these seals. However, after renewing the seals and sending a lot of oil into the pins, I see none coming out at the ends of the pins. Where is it going? To the insides of the springs. |
   
Laurie Fox
Experienced User Username: laurie_fox
Post Number: 27 Registered: 6-2004
| Posted on Friday, 13 October, 2006 - 08:47: |    |
Bill This post is in two parts. The first part was written before I saw your last post and I think I will let it go in that form. The second part then follows with more specific stuff. Part 1. In his first post in this topic, Bill says that he needs to sort out some of the pipe runs for the chassis lubrication system. In the region of the rear spring rear shackles there is a difference between the G series onwards and the earlier ones which is worth a mention. On the early cars (like mine) the flexible pipe connection on the chassis is in front of the shackle whereas on the later cars it is behind, towards the back of the car. The later cars have a longer flexible pipe (the only one now obtainable) and the position of the connection on the shackle itself is at a different angle. Because of this, fitting the longer flexible pipe to an early car requires some care so that, as the shackle moves over its working range, the flexible pipe is not strained and does not rub on anything. I have found that, on the shackle end of the flexible pipe, it is best to insert the minimum length of the copper pipe on the end of the flexible hose into the union on the shackle. This leaves a short, but sufficient, length of copper pipe out of the union for a slight bend to be made. With this small bend at that point the flexible pipe itself is not strained into too sharp a curve anywhere and does not pull at an angle on the shackle union as it otherwise would. The pictures below illustrate the point. B420EY has another modification to piping and this is the reason for the peculiar shaped bit of pipe above where the flexible pipe is attached to the chassis (second picture). This funny shaped bit is a rerouting of the pipe which feeds oil pressure to the nearside shock absorber bellows. On single exhaust MK VI's the original route of this pipe goes inside the chassis member close to the exhaust pipe. If the exhaust pipe is not quite in it's proper position it can rub on the copper pipe and eventually make a hole. When this happens the gearbox oil is pumped out (but only when the car is moving so it is not easy to detect) leaving about 2 pints if the car is level. In fact this is quite safe except on long hills going upwards since the largest gear on the second motion shaft is still touching the oil and swishes it around. But on alpine passes etc. this does not happen and, of course, the higher oil level at the back of the gearbox enables the pump to pump out even more oil. So if your gearbox suddenly wants four pints to top up instead on the usual minimal amount check that pipe.
Rear nearside. Car standing normally
Rear nearside. Spring on lower bump stop Part 2 I agree with your analysis, Bill. Richard has shrink-wrap on his springs which means that they are encased within an oiltight sleeve so no oil gets out until it reaches the point of attachment to the axle. Presumably his refined adjustment of the amount of oil delivered to various parts means that only the right amount is delivered to the lower rear shackle pin with virtually no excess. However, I would expect oil to emerge there after a while. Let us try to put some numbers to things. Assume that the central chassis pump will deliver 50cc of oil at 50 lb/sq in and that the pump piston seal is not leaking. The pipework maybe 8 metres in total length with 3mm bore. This gives a pipework volume of about 56cc. If the pipework is full of oil then the pump pressure will be available immediately at each of the restrictors. Each restrictor (which contains a spring loaded valve) will open as soon as the line pressure exceeds its opening pressure and pass oil until the line pressure drops to below the opening pressure setting for that particular restrictor. The amount of oil passed while the restrictor valve is open will depend on the restrictor on the supply side of the valve (a short length of wire in a standard diameter hole with the diameter of the wire being different for different restrictor ratings). If there is any air in the pipework to start with it will probably get pushed out with a few pumpstrokes anyway. There are about 26 restrictors in the standard system (ignoring the fact that the arrangements in the centre steering pivot are a bit different) so each restrictor would, on average, be passing about 2cc per pump stroke. So each end of each rear spring will be getting 2cc per pump stroke which is not a lot if it has to fill all the space within and around enclosed spring leaves. So, if the springs are shrink-wrapped or gaitered, oil may not come out for some time. But 2cc per pumpstroke will be going into the lower rear shackle pin and once the spare space has been filled it must come out past the sealing rubbers since there is nowhere else for it to go. But in practice things may be a bit different. The pressure at the pump probably remains at about what it should be but the volume of oil delivered may be less. I suspect that the spring loaded non-return valves in the restrictors vary a bit or may not be closing properly because dirt has got past the small filter pellet in each one. I think that Richard has these things in mind when he speaks about the system not necessarily being set up correctly at the works. But since this a total loss oiling system what goes in must come out somewhere and it is the visible coming out that evidences the going in at a particular point (maybe ignoring any oil which may get soaked up in the gaiters either temporarily or permanently). The pictures in Part 1 above show what oil gets out of my rear springs. There were taken in 2004 after I got my first digital camera and it was easier to photograph things like this. The rebuilt springs had been on for about four years. There is plenty of oil round the upper and lower shackles and not much drips off. I do one pump stroke about every 400 miles or so while on the move. There are slight drip marks on the garage floor which quickly get covered in dust and I look for signs of fresh drips from time to time, ignoring the dust covered stuff. The dust covered stuff gets cleared away every two years or so and does not amount to a lot. I can live quite happily with this situation since oil drips on the drive are quite rare. Lastly, for the moment, I must say that in the early days I did find some restrictors which had become completely bunged up and were passing no oil at all. The test for this was by uncoupling the restrictor but leaving it connected to the piping, operating the pump and seeing what came out. This was many years ago and if I had thought of it at the time I could have done this test with a new restrictor and this would have given me a better basis for the 2cc per pumpstroke estimate, which may be miles out. Regards Laurie |
   
Bill Vatter
Frequent User Username: bill_vatter
Post Number: 36 Registered: 9-2004
| Posted on Friday, 13 October, 2006 - 10:51: |    |
No need to buy new hoses. Keep the ends and replace the hose portion, or if there is nothing you can re-use, you can make up your own hoses with leftover bits from the bijur fittings box. That is what I did. Old bijur hoses are an example of things that should never be thrown away. The parts that are no good today may be all you can get tomorrow. |
   
Laurie Fox
Experienced User Username: laurie_fox
Post Number: 28 Registered: 6-2004
| Posted on Saturday, 14 October, 2006 - 00:45: |    |
Good point Bill. But they still have to be fitted properly to avoid unwanted strain and the tip might be useful to our less experienced viewers. |
   
Graham Squire Unregistered guest Posted From: 86.141.112.165
| Posted on Tuesday, 05 September, 2017 - 01:24: |    |
All good stuff above. Any tips on safe removal of rear springs and suppliers of replacement drip plugs?
(Message approved by david_gore) |
|