Author |
Message |
   
ross kowalski
Grand Master Username: cdfpw
Post Number: 602 Registered: 11-2015
| Posted on Tuesday, 17 October, 2017 - 09:42 am: |    |
I did the axle bearings on the shadow and took pictures along the way. Turns out that about halfway through, I came to the realization that this was one of those jobs where needing a tutorial basically means that you probably should not be doing it in the first place. I bought a set of axle cores off of e-bay and rebuilt those so when fitting came the car would only be down an hour or two for the R&I on the parts. There were a few things worth posting so here they are. You need to buy new keys. The woodruff keys in the taper were toast.
The vise I was using was pretty shabby and held on with a single 7/16 bolt and washer and a lag bolt (the third mounting had already been torn out). So if you think you need a special vise for 500 ft/lbs of torque, you don't. You do however need to support the socket with something against the yokes. I used the back end of a chisel, without that the socket would come right off I imagine.
This is the cleverish bit. To get the reqired torque, weight yourself, divide the desired ft/lbs (smoot/stones) by your weight and you get the number of feet from the socket you need to apply the force of your weight to generate the desired torque at the socket, wrap a wire around your pipe at that point and with the pipe horizontal stand on the wire loop.
BTw, the wire needed to be 6 inches closer to the socket for the correct torque. |
   
Patrick Ryan
Grand Master Username: patrick_r
Post Number: 1722 Registered: 4-2016
| Posted on Tuesday, 17 October, 2017 - 12:49 pm: |    |
Great stuff Ross, But you lost me on the last one. may need a video for that  |
   
Patrick Lockyer.
Grand Master Username: pat_lockyer
Post Number: 1573 Registered: 9-2004
| Posted on Tuesday, 17 October, 2017 - 05:02 pm: |    |
Ross will the torque figure decrease by the drag of the force due to resistance between socket and chisel and give an incorrect figure, lower than that required. Looks like the hub taper has been moving to cause the wear on the woodruff key maybe!
|
   
Paul Yorke
Grand Master Username: paul_yorke
Post Number: 1910 Registered: 6-2006
| Posted on Tuesday, 17 October, 2017 - 06:03 pm: |    |
That's what his extra 6" were for Patrick L For sure it has been moving, lucky it didn't shear! |
   
Patrick Lockyer.
Grand Master Username: pat_lockyer
Post Number: 1574 Registered: 9-2004
| Posted on Tuesday, 17 October, 2017 - 08:38 pm: |    |
Paul I thought the extra 6" closer was for the allowing of the extra weight beyond the wire of the bar. A higher torque figure attained with drag would mean moving the wire outwards. |
   
ross kowalski
Grand Master Username: cdfpw
Post Number: 603 Registered: 11-2015
| Posted on Wednesday, 18 October, 2017 - 10:02 am: |    |
Patrick L, The six inches closer to the socket just means I need to go on a diet. I did the calculations for just over the upper torque rating and the socket was covered in axle grease so I think I am OK on the torque. The keys on the core axles were bad. The o-rings were missing on both axles and replaced with silicone so someone was in there. When I removed the nuts I used a longer breaker and was surprised how tough they were to remove. 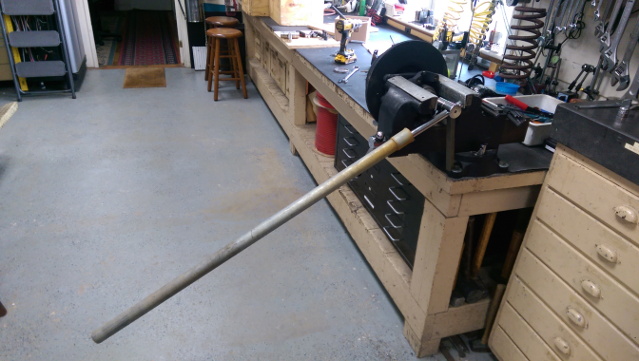 |
   
ross kowalski
Grand Master Username: cdfpw
Post Number: 604 Registered: 11-2015
| Posted on Thursday, 19 October, 2017 - 09:49 am: |    |
Patrick R, Here's a video, https://youtu.be/LxtFwesVZrE?t=54 Mostly it is the change in timbre of the tone when setting a bearing race. |