Author |
Message |
   
Benoit Leus
Prolific User Username: benoitleus
Post Number: 133 Registered: 6-2009
| Posted on Tuesday, 04 March, 2014 - 05:49 am: |    |
Recently the "2 brake pressure" light takes too long to go out. When the car has been standing for a few days it easily takes 30-60 seconds for the light to go out. Once it is out it doesn't come on again, even when leaving the car for a few hours and restarting it. The car brakes perfectly well I can find no leaks whatsoever. The accumulator and hoses have been replaced 5 years (5000miles)ago. I don't want to drive the car beore this issue is solved. Could it be the accumulator, altough not old, is the cause ? Benoit |
   
Brian Vogel
Grand Master Username: guyslp
Post Number: 733 Registered: 6-2009
| Posted on Tuesday, 04 March, 2014 - 06:11 am: |    |
Benoit, I'd suspect the accumulator is getting low on nitrogen. That being said, have you done the "brake pedal test" to see how many pushes you get before the warning light comes on? If you've got at least 30 presses I would not be overly concerned. My two cars vary in how long it takes for their respective lights to extinguish and that's with newly rebuilt accumulators. My System 2 light takes longer on both, particularly if the car has been sitting for an extended period, easily between 30 and 60 seconds. I still get 60 pumps before it illuminates when the brake pedal test is done. One thing I noticed is that when the accumulators are at least somewhat low, but not spent by any stretch, is that the "time of sitting" before a pressure light will illuminate is shorter. I am guessing that the ACV relies on the pressure from the accumulator when the car is off to keep itself firmly in the closed position. They seem to allow bleed off of fluid from the accumulator back to the reservoir itself a lot more quickly when the accumulators are not at peak pressure. What determines if the car is safe to drive is whether you would have enough pressure left in a stall situation so that you can stop the car (or at least that's my metric). Your best way to determine that is with the brake pedal test. Brian, who is certain that others' mileage will vary on this issue |
   
Jim Walters
New User Username: jim_walters
Post Number: 3 Registered: 1-2014
| Posted on Tuesday, 04 March, 2014 - 08:46 am: |    |
I have found on later Shadows that the pressure switches can get sticky with age. They are simply a disc of thick rubber that under pressure presses a steel disc to turn off the light. The switch comes apart easily, and a cleaning of the pieces inside often rectifies this symptom of slow warning light extinguishing. If your pedal pump down test shows the spheres to be well charged then it is possible it is just a dirty switch. Jim. SRE22493 NAC-05370 www.bristolmotors.com |
   
Brian Vogel
Grand Master Username: guyslp
Post Number: 734 Registered: 6-2009
| Posted on Tuesday, 04 March, 2014 - 10:05 am: |    |
Jim, I'm glad to hear you offer this observation. I rebuilt one of the pressure switches on SRH33576 in 2009, and thought at the time that all the rebuild kit seemed to do was loosen things up a bit. Over the course of years I'm sure that the crud that floats around in the hydraulic system, and there's always some, could easily deposit itself in the space where the plunger travels. These things are quite simple and I'd be willing to bet that more times than not a taking apart, cleaning up, and reassembly would get you right back to normal. The one that's up on top is also simple to get to so it's an easy experiment if that's the one giving issue. Brian |
   
Benoit Leus
Prolific User Username: benoitleus
Post Number: 134 Registered: 6-2009
| Posted on Wednesday, 05 March, 2014 - 05:27 am: |    |
Tonight I did the brake pedal test and the warning light came on after 45 pushes. Not great, but still ok I guess. When I restarted the engine, the light went out after a few seconds, so that was good. I then discovered that one of the hoses from the reservoir to the brake pump is "sweating". I suppose this could lead to a pressure loss when standing for a while. I'll replace this and see if it solves the problem. |
   
Jim Walters
New User Username: jim_walters
Post Number: 4 Registered: 1-2014
| Posted on Wednesday, 05 March, 2014 - 06:06 am: |    |
Benoit, this is the pump feed line and has no pressure nor would it have any bearing on pressure loss. If one hose is weeping, replace the other while you're at it. You can use generic EPDM hose. Below is a post from Brian Vogel regarding which hose to use: "Based upon JD's post last night I went in search of some EPDM hose at one of my local auto parts emporiums: Federated Auto Parts. Dayco Standard Heater Hose, 3/8" ID, part number 036687173331, and made in the USA is composed entirely of EPDM and is a virtually identical visual match for the OEM stuff in the car. It goes for the royal sum of 72 cents per foot" SRE22493 NAC-05370 www.bristolmotors.com |
   
Brian Vogel
Grand Master Username: guyslp
Post Number: 736 Registered: 6-2009
| Posted on Wednesday, 05 March, 2014 - 07:39 am: |    |
Benoit, If you're getting 45 pushes you're still well within the "safety zone" as far as accumulator reserve goes. I suspect that Jim's theory regarding the pressure switch may be the culprit. He's already pointed out that the hoses between the reservoir and the pump inlet is strictly gravity feed and there is no pressure involved on that side. This is the first time I think I've been quoted on how common the type of EPDM hose that can be used for these lines actually is. I can't imagine that 100% EPDM heater hose of the necessary diameter wouldn't be available at virtually any auto parts store. Brian |
   
Benoit Leus
Prolific User Username: benoitleus
Post Number: 135 Registered: 6-2009
| Posted on Friday, 07 March, 2014 - 05:50 am: |    |
I will certainly investigate the pressure switch, but there might be something else. The longer the car stands, the longer it takes for the dashboard light to go out. After 24hrs +/- 10 sec and after a week 60 sec easily. This might indicate that the braking system is losing pressure over this period. |
   
Brian Vogel
Grand Master Username: guyslp
Post Number: 741 Registered: 6-2009
| Posted on Friday, 07 March, 2014 - 08:06 am: |    |
Benoit, I do suspect that there is an "internal leak" from the ACV back to the reservoir. You can figure out if you have an this type of leak by looking at the reservoir after the car has been sitting for a while. The longer it sits the higher the fluid level will get in the reservoir in question. It's not unusual for the accumulators to lose fluid pressure (as opposed to nitrogen pressure) over the time periods you note. My personal experience is that the extinguishing time after sitting for a week can easily be 60 seconds if your accumulator does not have a perfectly full nitrogen charge. Your biggest concern, provided you don't have an external leak, is that you get at least 30 pumps on the pedal test. You've got plenty of reserve panic stopping power in the event of a stall if you've got 30 pumps or more. Perhaps I need to put together the article I've been meaning to write about making your own hydraulic pressure gauge, with all parts except the gauge itself very readily available and the gauge still awfully easy to source. Brian |
   
Bill Coburn
Moderator Username: bill_coburn
Post Number: 1529 Registered: 4-2003
| Posted on Friday, 07 March, 2014 - 05:46 pm: |    |
If I may pontificate, in my experience the pressure switch is your culprit Benoit. Ideally the accumulator operates between 1000 psi and 2,500 psi. The initial charge of nitrogen is 1000psi. Most recent tests I have done on pressure switches showed they have closed at about 900psi. If your car has been standing for days the pressure in your system should not be more than 1000psi although realistically it will be less. Let's say it is just below 900psi and you start the engine, in my experience the warning light has gone out before I have focussed on the dash board or the dirt on the windscreen! Just a few pumps from those little treasures in the block valley will very quickly ramp up the accumulator pressure beyond the cutout switch value! As Brian says the crud in these systems is amazing and where a reasonable electrical earth connection is required therein, one can only hope. Exhaust your systems with the brake pedal, take off the left front wheel and using a 1" UNF spanner release the switch, pull it to pieces clean it check it and refit it then report back! If you really want to investigate, make up a gauge and connection - the former are not expensive and the local brake shop will make the pipe and connection for you. Exhaust the system screw your new toy into the bleed hole and watch the gauge when somebody else starts the engine. The first 'bump up' reading will give you a fairly accurate reading on the nitrogen pressure holdings And then you can follow the instructions in the manual and get all the information you can need other than the number of the local lottery winning ticket! |
   
John Grieve
Experienced User Username: john116
Post Number: 27 Registered: 4-2012
| Posted on Friday, 07 March, 2014 - 09:54 pm: |    |
When I first acquired my SSII I completed an entire hydraulic system rebuild, except for the switches. Do you think I could get those two annoying red lights to go off consistently? One would flicker a bit, another would go off occasionally, but inconsistently with what they should have been indicating. I finally bought two new switches and installed them. Lights off more or less straight away after starting the vehicle, 60 pumps of the brake pedal before they both went off. I'd highly recommend cleaning them or replacing them before investigating anything else (unless you have an obvious fluid leak). |
   
Geoff Wootton
Grand Master Username: dounraey
Post Number: 365 Registered: 5-2012
| Posted on Saturday, 08 March, 2014 - 02:33 am: |    |
One thing I find really useful for any kind of work on the brakes/hydraulic system are male and female blanking plugs. These are used to plug hydraulic lines when they have been disconnected and are simply screwed into the hydraulic fittings. They do not negate the need for bleeding the system but they do prevent the drips of brake fluid from disconnected lines. These drips can accumulate to form quite a sizable loss of fluid over time, as can be verified by the fluid level in the container you have placed to catch the drips or by the size of the puddle on your garage floor. Makes bleeding much easier as there is much less fluid loss. |
   
Brian Vogel
Grand Master Username: guyslp
Post Number: 742 Registered: 6-2009
| Posted on Saturday, 08 March, 2014 - 02:38 am: |    |
To follow up on Geoff's point: In most cases extra bleed screws can serve perfectly well as blanking plugs. I've found it nearly impossible to find true blanking plugs in the US, but bleed screws are available everywhere. Since the whole purpose is to stop fluid flow from fittings where bleed screws can seat as well as a blanking plug you can use bleed screws in their place. To amplify Geoff's point, some of those openings don't just drip, they spout!! I own one real Crewe blanking plug that came in a 4-way connector that I bought as a used part. Brian P.S. to Geoff: What on earth is a female blanking plug? I'm having trouble wrapping my head around that concept. |
   
Geoff Wootton
Grand Master Username: dounraey
Post Number: 366 Registered: 5-2012
| Posted on Saturday, 08 March, 2014 - 02:49 am: |    |
I bought mine from a local specialist hydraulics shop. I agree, it is a bit "hit and miss" whether you can buy them locally. Certainly in Benoit's case I would recommend he uses an easily obtainable bleed screw to blank off the hole when he removes the pressure switch. Geoff |
   
Geoff Wootton
Grand Master Username: dounraey
Post Number: 367 Registered: 5-2012
| Posted on Saturday, 08 March, 2014 - 03:32 am: |    |
Hi Brian The best example I can find on the web of a female blanking plug is shown below. Mine are still packed away so I could not find them to take a photo.
They screw over the male hydraulic pipe fitting to form a seal. Have we hit on another UK/US terminology difference here. I thought the terms were widely used. |
   
Brian Vogel
Grand Master Username: guyslp
Post Number: 743 Registered: 6-2009
| Posted on Saturday, 08 March, 2014 - 04:16 am: |    |
Geoff, I don't know whether it's a US/UK terminology difference or a "what I'd call that not knowing what it's actually called" versus real name difference. Were I to be referring to the above pictured item it would be as a "blanking cap" or "sealing cap" as opposed to a plug. For me, a plug is "an outie" by definition that either threads into something or is pushed into an opening such as a bottle. Caps, conversely, screw on to "the outie" or snap over a protrusion. It's been interesting to me to see how the terms screw and bolt are used somewhat interchangeably in the Crewe documentation. For me, a screw must have an indentation of some sort on its head to allow the tool that turns it to thread it into whatever. For me, a bolt is a threaded fastener with a hex head, regardless of whether it's tiny or large, and regardless of whether it threads into something or simply passes through and is secured using a nut on its threaded end. If memory serves, and it may not be doing so, it seems that Crewe documentation considers any threaded fastener that threads into something a screw. Brian |
   
David Gore
Moderator Username: david_gore
Post Number: 1368 Registered: 4-2003
| Posted on Saturday, 08 March, 2014 - 08:27 am: |    |
Hi Brian, The following definitions from elsewhere in the world are recognised "Down Under":- Screw: Threaded fastener, usually tapered with drive adaptor indented in head. Bolt: Parallel threaded fastener, usually hexagon or square headed used with a nut and washers as appropriate to hold two or more components together. The hold may be rigid or allow rotation/sliding depending on what is required for the application. Stud: Parallel threaded fastener, usually hexagon headed but may also have a round head with indented drive adaptor [this is often described as a "cap screw" and Crewe used this term extensively for round-headed studs] used with washers as appropriate to hold two or more components together. The hold may be rigid or allow rotation/sliding depending on what is required for the application. The essential difference between a stud and a bolt is the stud goes into a threaded hole in one or more of the components for retention rather than into a nut. Male fitting: For reasons relating to human interaction between the sexes, this refers to any fitting that has an external thread. Female fitting: For the same reason given above, this refers to any fitting that has an internal thread. As the early engineers were almost entirely male, it is easy to comprehend why the usage of these descriptions quickly became universal . |
   
Bob Reynolds
Frequent User Username: bobreynolds
Post Number: 65 Registered: 8-2012
| Posted on Saturday, 08 March, 2014 - 02:37 pm: |    |
There is no universal definition between a screw and a bolt. For instance, what about a machine screw, or a set screw? Are they really bolts? One definition says that a screw is threaded for its entire length, whilst a bolt has an unthreaded portion. Another says that a screw screws into a tapped hole, whilst a bolt screws into a nut. However, the best definiton I have seen is this: If a screw is overtightened the threads will strip, whereas if a bolt is overtightened its head will shear off! |
   
David Gore
Moderator Username: david_gore
Post Number: 1369 Registered: 4-2003
| Posted on Saturday, 08 March, 2014 - 03:12 pm: |    |
My rationale for distinguishing between a screw and a bolt is the fact a screw will cut its own thread when entering a pre-drilled hole whereas a bolt will not [however, as we all know, a misaligned bolt will destroy a thread]. The introduction of self-drilling screws for fastening timber, plastic and sheet metal facilitates this characteristic by eliminating the need to pre-drill. With regard to over-tightening, whether the thread strips or the bolt/screw shears is more a function of the length and pitch of the engaged thread than anything else; short engagement makes stripping more likely, long engagement makes shearing more likely. For what is is worth, I have sheared the heads off screws by over-tightening more times than I care to admit. |
   
Kelly Opfar
Experienced User Username: kelly_opfar
Post Number: 20 Registered: 7-2004
| Posted on Sunday, 09 March, 2014 - 12:03 am: |    |
According to the American Society of Mechanical Engineers (ASME) standard B18.2.1, a bolt is inserted into a hole and secured with a nut, whereas a screw is inserted in a threaded hole - sometimes along with a nut. |
   
David Gore
Moderator Username: david_gore
Post Number: 1370 Registered: 4-2003
| Posted on Sunday, 09 March, 2014 - 10:07 am: |    |
Trust the Yanks to "try and reinvent the wheel" ...... I far prefer the traditional definitions from the home of the Industrial Revolution where the invention and refinement of mechanical fastening technology played a major role in the massive changes that occurred during and after this Revolution. |
   
John Kilkenny
Prolific User Username: john_kilkenny
Post Number: 160 Registered: 6-2005
| Posted on Sunday, 09 March, 2014 - 11:41 am: |    |
If this thread keeps going I suspect it soon will be discussing how many angels can sit on the head of a 6BA screw (or bolt) LOL. Kelly's ASME definition is simple and should not require further embellishment. |
   
Jim Walters
New User Username: jim_walters
Post Number: 6 Registered: 1-2014
| Posted on Sunday, 09 March, 2014 - 02:35 pm: |    |
Brian, brake hose end caps readily available here: http://www.aircraftspruce.com/categories/aircraft_parts/ap/menus/ha/an.html These are the ones I have and they work great. You want the 3/8ths X 24 ones. Aircraft Spruce is a good source of high quality hardware. SRE22493 NAC-05370 www.bristolmotors.com |
   
Brian Vogel
Grand Master Username: guyslp
Post Number: 744 Registered: 6-2009
| Posted on Monday, 10 March, 2014 - 08:52 am: |    |
Jim, Thanks. Have added that to the resources file. It appears that AN 3D size caps are the correct ones. 3/8-24 for a 3/16" diameter tube. Each cap for the princely sum of $2.17 US. When I compare this to $17.81 each for a UE10378 ACV crush washer I can only be extremely pleased. Brian, who has subsequently had twenty UE10378-type crush washers custom machined for a hair more than the cost of one Crewe Original |
   
Benoit Leus
Prolific User Username: benoitleus
Post Number: 136 Registered: 6-2009
| Posted on Monday, 10 March, 2014 - 06:27 pm: |    |
Continuing the "brake pressure warning lights" saga, I also discovered a problem with the "1 brake pressure" light. The light itself works, as it goes on when starting the car, but when exhausting the system with the "pressing" method, it doesn't come on. I gave up after 170 times, as my leg began to get sore. Could this also be a brake pressure switch problem ? I ordered some new washers and will clean them out over the weekend. |
   
Brian Vogel
Grand Master Username: guyslp
Post Number: 745 Registered: 6-2009
| Posted on Tuesday, 11 March, 2014 - 12:35 am: |    |
Benoit, Yes. If the lamp works during the "start up test" but never comes on after pressing the pedal you most likely have a pressure switch problem. It sounds like your System 1 switch is stuck in the "pushed open" position and never springs completely back when system pressure is removed. The lights typically come on fairly close to one another during the pressing test. I've never seen more than 20 pumps difference and System 1 has had a general tendency to come on before System 2 in my experience. Brian |
   
gordon le feuvre
Experienced User Username: triumph
Post Number: 28 Registered: 7-2012
| Posted on Thursday, 13 March, 2014 - 05:45 am: |    |
GOING BACK TO THE ORIGINAL QUERY, THE SWITCHES DO GIVE PROBLEMS. ALSO IF THERE IS NO NITROGEN, THE LIGHTS WILL GO OUT AS NORMAL ON STARTING, BUT WILL COME ON WITH THE FIRST APPICATION OF BRAKE (ASSUMING SWITCHES ARE WORKING CORRECTLY).MY EXPERIENCE WITH LIGHTS TAKING TOO LONG TO EXTINGISH IS THAT THE INTERNAL DISC/BALL BEHIND SPRING IN THE VALVE BODY LEAKS INTERNALLY CAUSING FLUID TO BE BETURNED TO THE RESERVIOR BEFORE THE PRESSURE IS UP TOWARDS THE 23-2500 PSI. THIS CAN BE CHECKECED OUT BY REMOVING THE RETURN RUBBER HOSE OFF THE VALVE BODY AND SEEING IF IT STARTS TO RETURN FLUID TO RES. AS SOON AS ENGINE STARTED (HAVING FIRST BEEN DE-PRESSURISED)THE PUMP IS EFFECTIVELY FIGHTING ITSELF. THERE REALLY IS NO SUBSITUTE TO OBTAINH A GAUGE AND PUTTING INTO VALVE BLOCK-NOT IN BEED SCREW BUT IN OUTPUT PIPE AS THIS ELIMINATED ACCUMULATORS FROM REST OF SYSTEM(MORE INPORTANT IN REAR AS THIS ACTIVATED HEIGHT CONTROL) Do be warned that if return pipe is taken off and system is working correctly, as soon as pressure reaches desired level2000+ fluid WILL squirt out under pressure as valve body redirects pump pressure from sphere to reservoir |
   
Benoit Leus
Prolific User Username: benoitleus
Post Number: 137 Registered: 6-2009
| Posted on Thursday, 13 March, 2014 - 11:31 pm: |    |
Can anyone identify the hose in these pictures. It leaks a little bit and I do have the impression it is brake fluid. Maybe it is related to the brake warning light issue.
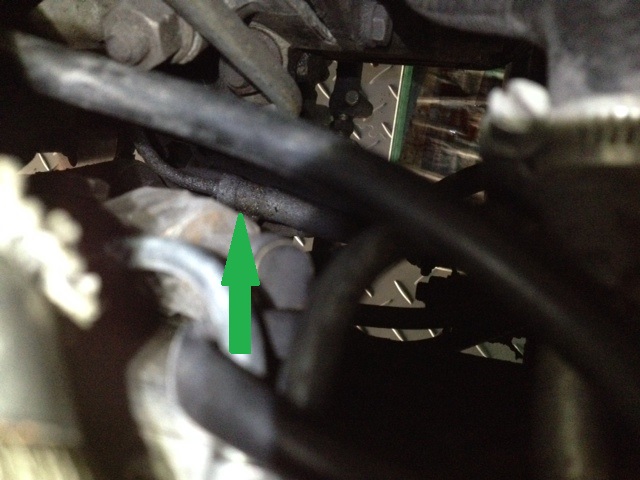 |
   
Benoit Leus
Prolific User Username: benoitleus
Post Number: 138 Registered: 6-2009
| Posted on Thursday, 13 March, 2014 - 11:35 pm: |    |
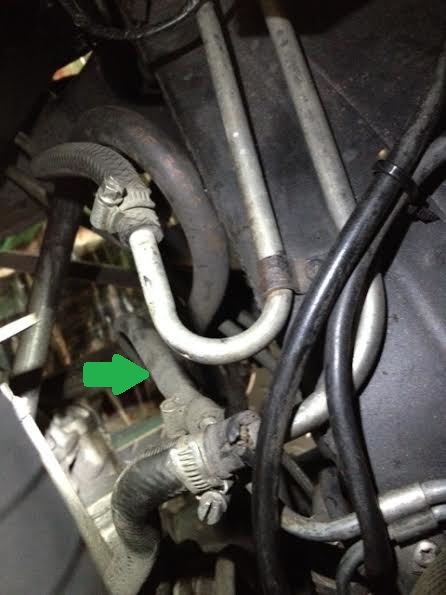 |
   
Brian Vogel
Grand Master Username: guyslp
Post Number: 748 Registered: 6-2009
| Posted on Friday, 14 March, 2014 - 12:17 am: |    |
Benoit, It's very hard to orient myself with those pictures (and I know it's difficult to decide how close for detail and how far for scope). There are only 2 brake lines per system in the collection that are "virtually no pressure" and secured with jubilee clips/hose clamps: the gravity feed from the reservoir to the pumps and the return line from the accumulator control valve to the reservoir. I can't see the origin of the tubing in the first photo, but I suspect it may be the low pressure return line from the ACV. If that's what it is, and it looks like it's old, it's missing a jubilee clip at the lower end and could easily begin to drip fluid over time. When new the grip of the rubber on the tube is quite sufficient to prevent leaking but as the rubber ages, hardens, loses elasticity and gets shaken about leaks can occur - hence the clip. In either case, these two lines are not involved in the pressurized portions of the system and have nothing to do (in any direct sense, unless your gravity feed to the pump is blocked) with whether the system pressurizes or not. Brian |
   
Brian Vogel
Grand Master Username: guyslp
Post Number: 749 Registered: 6-2009
| Posted on Friday, 14 March, 2014 - 12:32 am: |    |
Gordon, Why does it make any difference if one puts the pressure gauge in the bleed screw port (which is what the workshop manual recommends) or the output line to the system, as these two ports share a common source? I also find it easier to check whether the system is doing its flick-up, etc., without ever taking off the return hose to the reservoir. You will never see the correct cut-out, fall-back, and cut-in pressure behaviors if the ACV is allowing open or "semi-open" flow back to the reservoir prior to normal pressurization. These are all accurately read using the bleed screw port. Brian, who once made the mistake of opening the bleed screw on the pressure switch without a fluid catch at the ready - never again! |
   
Paul Yorke
Grand Master Username: paul_yorke
Post Number: 1171 Registered: 6-2006
| Posted on Friday, 14 March, 2014 - 05:14 am: |    |
Benoit, that appears to be the low pressure return hose. There is a flow chart for checking the accumulator and hydraulic systems. Should be in your manual. Brian, you cay correctly that the ports open to the same chamber, and you can read the same pressures from both. HOWEVER . . . You need to do both, Put it in the bleed screw port first and test it there. If ALL OK then that's fine, testing ends there. If things are NOT OK then there could be an internal leak through the accumulator OR through the cars brake or suspension system. (or indeed both) Your next step is a gauge in the HP pipe outlet instead. You will then be PURELY testing the accumulator and valve systems. Do the same tests and if the results are the same as before, then the fault (or main fault) is with the accumulator valve / Pump / accumulator. (Because you have isolated it from the rest of the vehicle.) If the fault is cured by using the HP hose outlet , then the fault lies somewhere in the rest of the vehicle. |
   
Brian Vogel
Grand Master Username: guyslp
Post Number: 750 Registered: 6-2009
| Posted on Friday, 14 March, 2014 - 08:32 am: |    |
Paul, Thanks for the clarification regarding when the high-pressure output port should be used as opposed to the bleed screw port. I have not yet (knock wood, kind words to God) encountered an ACV failure. Issues were always with the accumulator and/or the pressure switch. I know dead/dying pumps can happen but I'd presume that you'd see a glacially slow climb from flick-up to cut-out pressure (if it even makes it to cut-out) via the bleed screw port if the pump's bad. I've rebuilt three ACVs since "they were due" and I was there already. I was actually shocked at how simple they are compared to what I'd expected based upon the documentation. Fault diagnosis on these cars is filled with subtleties, particularly when it comes to the very rare failures. I sometimes fall prey to ignorance and/or the willingness to dismiss the unlikely, at least until "the usual checks" have been made. |
   
Paul Yorke
Grand Master Username: paul_yorke
Post Number: 1172 Registered: 6-2006
| Posted on Friday, 14 March, 2014 - 07:34 pm: |    |
If you read through all the steps and possibilities when you have time (before carrying out the tests) it should hopefully give insight into what's going on, and why the various steps are needed. This one is from the Shadow II manual and I haven't the time to check it all now/ Hopefully it is the same as the Shadow I flow chart. (It should be). Sorry, they are PDF's not sure why they are not posting correctly. |
   
Brian Vogel
Grand Master Username: guyslp
Post Number: 752 Registered: 6-2009
| Posted on Saturday, 15 March, 2014 - 01:37 am: |    |
Paul, Thanks for posting that. I already have a hard copy from the Shadow Hydraulics Workshop I took from the RROC-US/Rolls-Royce Foundation in 2006. I've done most of this so many times now that some of it has "become intuitive." I've been lucky in that I have never had to do every single step in the flowchart. I think I've never made it beyond a cyclic "Operation 2." This was one of the better, if not the best, step-by-step work flow charts for a complex task I've ever seen. The only "improvement" I would make to it, given the age and condition of many Shadows that have been allowed to sit forever, is that "Operation 1" should start with, "Remove the cover and baffles from the reservoir to check the condition of the fluid and mesh filters in the reservoir." What I've seen in these after long periods of "rest" is nothing short of horrific. The reservoir in SRH33576 looked like this the first time I opened it (and I'll note that this was only 2 years after I'd had several thousand dollars of brake work done by a well-known RR specialty shop that I shan't ever frequent again):
and LRK37110's looked like this:
and that was after a full hydraulic system overhaul by a shop that had and still has a sterling reputation, but followed by immediate hibernation afterward for between 5 and 6 years. RR363 does not like sitting. I've often really wondered what creates the stuff that looks for all the world like algae. Brian |
   
Randy Roberson
Prolific User Username: wascator
Post Number: 178 Registered: 5-2009
| Posted on Sunday, 16 March, 2014 - 11:24 am: |    |
Comment on the sources for EPDM non-pressurized return hose: I bought some at Tractor Supply, very inexpensive. Seems it is commonly used for low-pressure agriculture sprayers (herbicide, insecticide) and it was an exact replacement for that on my car. An agriculture supplier who deals in sprayers, then, can be a handy source. I will replace the reservoir feeds to the pumps when I overhaul. |
   
Brian Vogel
Grand Master Username: guyslp
Post Number: 753 Registered: 6-2009
| Posted on Sunday, 16 March, 2014 - 11:44 am: |    |
Randy, If you don't already know this, dirt common EPDM heater hose of the correct diameter is readily available at virtually any auto parts store and is a direct replacement for the gravity feed hoses between the reservoir and the pumps. Brian |
   
Randy Roberson
Prolific User Username: wascator
Post Number: 179 Registered: 5-2009
| Posted on Tuesday, 18 March, 2014 - 02:02 am: |    |
Brian, interesting mention of algae; I wonder if there is some sort of microbe which can grow in the brake fluid? I know in industrial cooling systems, even treated with chemicals, sometimes a wad of bio-slime will form and it can cause all kinds of trouble. Glycol-based coolants are said to not support biological growth, and brake fluid is one of the glycols. When I opened mine up, it was not pristine, but it was nothing like this, and it was at least 3 years old then with very limited run time. I said before: if we could control moisture entry through the reservoir vents, that would have to help a lot, but there is very limited room between the bonnet and the reservoir to attach anything, and I do not want to modify the reservoir in any permanent way. There are dessicant devices which attach to tank vents for just this purpose, used in industry. I also use the hose clamps intended for auto fuel injection system hoses as they are well made, intended for hoses and seem functionally equivalent to the Jubilee clips (i.e. no slots). |
   
Benoit Leus
Prolific User Username: benoitleus
Post Number: 147 Registered: 6-2009
| Posted on Monday, 28 April, 2014 - 06:00 am: |    |
I replaced both brake pressure switches as one was sticking and the other didn't work at all. The number 1 switch now works fine and passes the brake pedal test with over 70 pumps. However, the sticking switch on the number 2 system poses a new problem. Before replacing it I could push the brake pedal 45 times before the warning light came on. With the new switch it comes on after only 7 pumps. I can see no obvious leaks and the car brakes normally. Bleeding the switch didn't help and I found the fluid to flow out of the switch very slowly and no airbubbles in it. This surprised me as I expected some air after installing the new switch. The accumulator was replaced 5 years and 5000 miles ago, so I would expect it to still hold enough pressure. Benoit |
   
Randy Roberson
Prolific User Username: wascator
Post Number: 217 Registered: 5-2009
| Posted on Monday, 28 April, 2014 - 07:23 am: |    |
Oh, maybe there is a problem with the pump associated with that switch. That is the reason I could not get one of my red lamps to go out. as for blanking plugs, I made one out of an old female nut with a short piece of flared tubing. I crimped the end of the tubing and it at least seals non-pressurized lines very well. |
   
Paul Yorke
Grand Master Username: paul_yorke
Post Number: 1189 Registered: 6-2006
| Posted on Monday, 28 April, 2014 - 08:27 am: |    |
Run the engine for 5 mins. Turn off. Open bleed nipple on accumulator and measure the amount of fluid that rushes out. It could be the pump, valve or accumulator. 5 years is a little soon, but not unheard off. Mileage is pretty irrelevant though. |
   
Benoit Leus
Prolific User Username: benoitleus
Post Number: 148 Registered: 6-2009
| Posted on Tuesday, 06 May, 2014 - 07:18 pm: |    |
I haven't had time yet to do the test that Paul suggested, but over the last 2 weeks the problem has gotten worse. Now, even after leaving the car standing for only 30 minutes, the number 2 system warning light will come on. When starting, it will go out within seconds and stay out, until I leave the car standing again for at least 1/2 hour. Again, the brake pumping test will never allow for more than 7 pushes of the pedal before the light comes on. 2 months ago I could I could leave the car standing for at least 2 days and the brake pumping test would allow for more than 40 pushes. I checked thoroughly for leaks, but can't find any, with the exception of a small dribble from the distribution valve. I'm just wondering : would a accumulator low on pressure deteriorate so quickly over a period of 2 months ? |
   
Benoit Leus
Prolific User Username: benoitleus
Post Number: 149 Registered: 6-2009
| Posted on Friday, 09 May, 2014 - 03:25 am: |    |
I followed Paul's advice and ran the engine for 5 mins, attatched a clear tube to the B-bank accumulator and opened the bleed nipple. Brake fluid flowed out quite strongly which suggests good pressure. I ran the engine again for 5 mins and did the brake pedal test. Now the light came on after only 5 pushes. However, I noticed something : previously, I had removed the rat trap cover when checking for leaks and cleaned up a few drops of brake fluid hanging from the distribution valve. After the brake pedal test, I noticed that there were again several drops hanging from the distribution valve, although I had only pushed the pedal 5 times. I now the distribution valves are supposed to leak a little bit but as much as this after only a few pushes of the brake pedal ? |
   
Brian Vogel
Grand Master Username: guyslp
Post Number: 778 Registered: 6-2009
| Posted on Friday, 09 May, 2014 - 05:41 am: |    |
From my perspective all signs suggest a depleted accumulator. It is quite possible for an accumulator to have pressure well below the amount necessary to extinguish the warning light and to still push out quite a bit of fluid. Although your leak from the distribution valve of several drops is "high" if they're all from only this brief interval, you'd have to have fluid leaking far faster than this to deplete the pressure in a fully charged accumulator in 5 pushes. I will be shocked if this doesn't turn out to be a loss of nitrogen charge. I had one of mine deplete over the course of several months when the main ball bearing "seal" and the secondary PTFE ball "seal" didn't and the tertiary o-ring seal was inadvertently omitted from the charge port cap. The improved sealing set up used in the Flying Spares accumulator rebuild kit appears to be a vast improvement over the original. Brian |
   
gordon le feuvre
Experienced User Username: triumph
Post Number: 34 Registered: 7-2012
| Posted on Friday, 09 May, 2014 - 05:54 am: |    |
I would not worry too much about leakage from the distribution valves. It was the very first service bulletin in 1966 saying do NOT change valves for drips off them! When the system has no nitrogen, the pressure flicks up to max straight away (the light goes out),but the light will come on with FIRST application of pedal. The amount of presses required to bring lights on gauges the amount of nitrogen in sphere. 45+ is good, less than 10-15 is poor. This ALWAYS assumes the pressure lights are working correctly, which sometimes can be hard to confirm. |
   
Paul Yorke
Grand Master Username: paul_yorke
Post Number: 1193 Registered: 6-2006
| Posted on Friday, 09 May, 2014 - 08:43 am: |    |
it's not the speed it comes out, it's the quantity. you should get at least 1/4 pint of fluid rushing out, preferably more. maybe around 1/2 pint.. I also wouldn't worry about the drips atm. |
   
Benoit Leus
Prolific User Username: benoitleus
Post Number: 150 Registered: 6-2009
| Posted on Saturday, 10 May, 2014 - 01:54 am: |    |
I redid the test Paul suggested and the amount of fluid coming out is way short of what it should be, so I guess it's indeed the accumulator. I'm just surprised and didn'texpect it as it was replaced only 5 years ago. I guess it might be wise to replace the valve seals at the same time ? |
   
Brian Vogel
Grand Master Username: guyslp
Post Number: 779 Registered: 6-2009
| Posted on Saturday, 10 May, 2014 - 05:19 am: |    |
Benoit, My own personal experience is that it's not possible to remove the accumulator without the accumulator control valve (ACV) coming out with it as an assembly. I would be happy to have someone post a set of instructions for getting one off of the ACV alone, as that can save a lot of trouble in certain circumstances. As I previously mentioned, I had an accumulator that lost its charge in a few short months due to the "old style" sealing that didn't and a missing tertiary o-ring seal. I would have to imagine that its entirely possible for an accumulator to leak at a rate such that 5 years would be its functional service life. That being said, the diaphragm should certainly still be intact (unless it's punctured, which is unlikely) and have a service life of much longer than 5 years. Were I you, I would remove the offending accumulator and recharge it. Be certain that a nylon or PTFE ball is used as a secondary seal at the charge port and an O-ring is placed inside the cap before you tighten it on. If the ball bearing that serves as the primary seal leaks, which happens frequently, and the stream of nitrogen is such that you can't put the PTFE ball in the charge port opening, you can put it in the small divot that's usually in the center of the inside of the charge cap then screw the cap on while it's pointed directly upward and the charge port directly downward. You will, of course, need to check for leaks at the charge port, around the center ring (very unlikely), and at the fluid entry point at the top. Were you to have a ruptured diaphragm you won't be able to charge the accumulator since the nitrogen will just come out of the opposite side at the fluid entry point. If you have to pull the ACV at the same time and you don't know when it was last overhauled I would definitely replace the O-rings. My experience is that a number of the parts included in the overhaul kit are not absolutely necessary in many instances. Two good examples are the little fluon ring that's part of the "piston and sealing ring" and the fluon bit on the end of the non-return valve have virtually perpetual lives, as do the sealing disc beneath the valve sealing plug (which uses an O-ring) and the regulator valve disc (the thing that appears as though it has a tiny ball bearing embedded in the middle and that seats in a tiny opening in the bobbin). I was terrified of the ACV based on available documentation but have to say it's much easier to rebuild than one might think. I can send you photographs of one of the ones I've rebuilt in "laid out as if exploded" view so you can see they're not all that intimidating. Brian |
   
Geoff Wootton
Grand Master Username: dounraey
Post Number: 384 Registered: 5-2012
| Posted on Sunday, 11 May, 2014 - 12:49 pm: |    |
Benoit You could try recharging the accumulator in-situ. After 5 years the nitrogen loss may have been due to gas permeation across the diaphragm, which means an in-situ re-charge would probably be good for another 5 years. if you remove the charging cap and find that the area is dry i.e. no brake fluid present, then the diaphragm is most likely undamaged. Geoff |
   
Brian Vogel
Grand Master Username: guyslp
Post Number: 780 Registered: 6-2009
| Posted on Monday, 12 May, 2014 - 02:34 am: |    |
Geoff, This is another of those differences between the SY1 and SY2 series cars. The SY1 cars have both accumulators mounted on one side with the charge ports pretty much "pointing directly down" allowing easy access for in-situ charging. The SY2 cars have one accumulator per side, mounted on a distinct tilt, and such that access to the charge port is well-nigh impossible in-situ. There's a good article on this in Tee-One Topics, Issue 21 entitled Topping Up the Accumulators. If memory serves, Benoit's car is a SY2 series (but I could be wrong). Brian |
   
Geoff Wootton
Grand Master Username: dounraey
Post Number: 385 Registered: 5-2012
| Posted on Monday, 12 May, 2014 - 07:00 am: |    |
Hi Brian Thanks for the correction. I've just checked and indeed Benoit's car is the SY2. Geoff |
   
Benoit Leus
Prolific User Username: benoitleus
Post Number: 152 Registered: 6-2009
| Posted on Tuesday, 13 May, 2014 - 04:58 am: |    |
Geoff, Brian, my car is indeed a Shadow 2. I'm afraid I will indeed have to take the accumulator off. Brian, I would be very gratefull for the photographs of a dismantled valve. I'll send you a private mail with my details. Regards, Benoit |
   
Benoit Leus
Prolific User Username: benoitleus
Post Number: 154 Registered: 6-2009
| Posted on Thursday, 29 May, 2014 - 07:39 pm: |    |
Just a quick update : replacing the accumulator and rebuilding the accumulator valve solved the problem. It took me some time to realize I had to remove the oil dipstick before being able to pull the accumulator out though. Thanks everyone for all the help. |
   
Michael Mangan
Unregistered guest Posted From: 69.35.203.238
| Posted on Saturday, 28 February, 2015 - 03:57 am: |    |
Hi Guys , I have just been reading all the fascinating posts. I have a 1972 LWB LRA14501. It just was in for servicing and I see a light I never saw before, it is at the top of the facia above the clock.It says "partial brake failure". I have looked in many books, and websites and never seen one. However I just found an illustration in the Brooklands book Silver Shadow 1965-1980. When I bought the car it was covered with black tape,but that was removed when it was in the shop. I'm uncertain how to proceed with it. Any suggestions ? Was it covered in frustration? Was it used on the facia for a very short time? Its not in the handbook.
(Message approved by david_gore) |
   
richard george yeaman
Prolific User Username: richyrich
Post Number: 263 Registered: 4-2012
| Posted on Saturday, 28 February, 2015 - 09:04 am: |    |
Hi Michael when I bought my 1974 Shadow I too found some black tape covering some of the lights on the instrument panel put there by some dodgy car dealer in the past or a previous past owner not necessarily the last one. All the lights should come on when the ignition is turned on and go out when the engine starts any that don't go out or takes too long should be investigated hopes this helps. Richard. |
   
John Kilkenny
Prolific User Username: john_kilkenny
Post Number: 185 Registered: 6-2005
| Posted on Saturday, 28 February, 2015 - 09:25 am: |    |
Michael, The Partial Brake Failure Lamp will come on if any of the four Brake Warning Lamps is energised. If it comes on by itself it indicates a failure of at least one of the four warning lamps. It will also light when the Lamp Rest Relay is operated. To cover a warning light with black tape is suspicious. |
   
John Kilkenny
Prolific User Username: john_kilkenny
Post Number: 186 Registered: 6-2005
| Posted on Saturday, 28 February, 2015 - 09:33 am: |    |
Re my previous post. Lamp Rest Relay should be Lamp Test Relay of course. |
   
Bob Reynolds
Prolific User Username: bobreynolds
Post Number: 239 Registered: 8-2012
| Posted on Saturday, 28 February, 2015 - 05:31 pm: |    |
I mentioned this lamp in a previous post. It is shown on the circuit diagram as 'part brake failure' but my 1975 Shadow does not have it fitted. It is connected to the other 4 brake warning lamps by diodes, so it lights up whenever any of the other lamps lights up. Can't see any point to it. |
   
Bob UK Unregistered guest Posted From: 94.197.120.140
| Posted on Saturday, 28 February, 2015 - 09:31 am: |    |
The original posting. This is very straightforward. All hydraulic systems have internal leaks and a lesser external leaks. 60 seconds for lights out is fine and probably quicker than most. note RR says 4 mins before checking the tank. Maybe so long due to rear rams. Mine is a little slower but my switch pressures could be higher than this car. The switches seem to change pressure and go either way due to dot grunge. A clean out fixes. However unless the exact lights out pressure is known then a gauge is required it doesn't matter which hole. Even a caliper will do if the brake is held on. For convenience use either the acv nipple or output union. I use the nipple. ALSO IF THE PEDAL IS HELD DOWN AS THE ACV CHARGES THE PRESSURE WILL TRY TO PUSH THE PEDAL UP stop shouting. Mine is quite forcefull and a daily indication that the brakes work. Citroen sometimes calls the brake valve a dozzer valve because its impossible to hold the pedal. It's not just RR systems that require proper clean care the other makes are the same. Get dirt in any brakes and it will damage something. Many cars have rear rams that work the same as RR, except the pump is electric or connected to the steering pump. Because no2 supplies the rams it will lose pressure quicker than 1 especially if the car is wobbled about when parked. My lights go out at around 1500psi which is nice and safe. It takes 2 days for no2 and 3 days for no1 to deplete down to 1000psi and a week to zero. 90 and 85 pumps to 500psi. Even at 500 psi there's enough brakes to stop. the gauges are £7.50 plus an adaptor and short brake hose or a bit of knufir. It's easy to understand and minutes to check it's a standard part of a brake check. To blank off pipes use a spare nipple or 1/4 ball bearing in the flare and clamp with union. Or small length of knufir squashed ans soldered for testing only. I have a small box with a gauge and blanks which costs £20 tops. One test is to fit gauge to caliper and measure the weight on the pedal to get say 500 psi. Fit gauge to the master cylinder caliper and 1500 psi is easy. If one does these easy quick test then you can be very certain that the system is good. I guess 20 pumps to 500psi is safe and 3 pumps is an mot pass. So I didn't worry about brakes But because 3 pumps is simply lost by lots of braking best fit new spheres. My brakes feel nice and dependable and never give trouble I maintain exactly like a normal car. Once a big brake service is done it should last 10 years or more. In professional garages it a simple days work Bish bash bosch and the jobs done a quick 20 mile road test and get paid. I have done 2 shadows loads of other cars and its all the same. Their are no snags or complications to me it's obvious. Its well designed and no harder than any other car. Just more pipes and bits. only annoyance is rear rams but they always come out in the end. My rams are 40 years old and work fine. I need new ram flexibles at the moment because they are 40 years old. £10 each and 10 minutes work a quick bleed and a dash of dot The New hoses will make the rams Work quicker but will deplete no2 quicker. Kiss------- keep it simple Hope this gives people the notion of how simple the hydraulics actually are. The professionals on this forum will know what I mean. Try this,using Microsoft paint draw the system out in colour once done you will understand so much more. My one is exactly like my car and the first drawing is the complete system then using copy and pasted the system is separated into the separate bits showing ride height only etc. A quick glance refreshers me instantly. The drawings show flexibles sizes etc. Which allows me to accurately buy hoses without even taking parts off. Also I always have a roll of kunfir in a box with spare unions pipe cutters and benders and flare tool and 7/16 And 3/8 spanners and sockets. Fits most bit cars. I keep the gauge and spares on a separate shelf along with dot oil and rubber grease. I keep the Microsoft drawing filed in with the brake chapter. Not sure but I read somewhere that 40 lbs of pedal pressure should be 500 psi at the calipers, sounds about right. Notice how long the pedal is to the pivot and how short the levers are, twice that of normal cars. Its so simple and well made it can't really go wrong. Bish bash bosch next car please Otherwise the garage goes bust.
(Message approved by david_gore) |